- By Oliver Haya
- August 05, 2024
- Rockwell Automation
- Feature
Summary
Understanding energy consumption patterns is the bedrock of effective energy management.
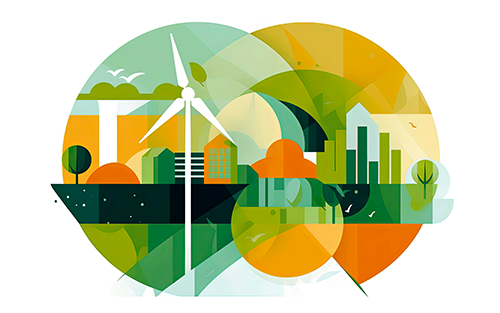
From countries to businesses to individuals, tackling climate change is now a major focus. Rising energy costs and demand, the digitalization of energy networks, the need to optimize efficiency and increasing regulations are pressure points driving greater emphasis on energy management.
In the manufacturing sector, skyrocketing energy costs are compelling companies to boost efficiency. With global electricity demand set to triple by 2050, strategic energy management is no longer optional but critical for maintaining operations. Moreover, as industries strive for "net zero"—balancing greenhouse gas (GHG) emissions with removals—energy management has become a cornerstone of operational success.
Understanding energy consumption patterns is the bedrock of effective energy management. Manufacturers aiming to cut costs, enhance sustainability, and adapt to evolving regulations need robust programs that reveal the where, when, and how of their energy use. This insight not only pinpoints areas for savings but also helps define key performance indicators, guiding their journey toward a leaner, greener future.
Untangling the data web
In the past, energy data collection was a maze, thanks to fragmented networks and isolated data silos. This disjointed setup made it nearly impossible to extract precise energy metrics from individual machines, as the data lacked crucial Operational Technology (OT) context. Most manufacturers were left with just a monthly snapshot of their facility's total energy use—a blunt tool for a job requiring surgical precision.
Smart energy management demands a panoramic view of consumption, focusing on the "WAGES" element: water, air, gas, electricity, and steam. Each component carries its own carbon weight and price tag. To navigate this complexity, companies must first map their greenhouse gas (GHG) emissions across three domains:
- Scope 1: Direct emissions from owned or controlled activities
- Scope 2: Indirect emissions from upstream processes
- Scope 3: Indirect emissions tied to a product's lifecycle
To hit global sustainability marks, businesses must trim all three scopes. The first step? Establishing an energy baseline - gauging current carbon output and identifying reduction opportunities. Yet, a major hurdle persists - manufacturers typically receive lump-sum utility bills, making it tough to pinpoint which products drive specific energy costs. The solution? Drill down to the device level, tapping into granular WAGES data from individual sensors.
But raw device data is just the start. It needs to be woven into the broader factory narrative. Which energy meter corresponds to which product line, and when? How does product loss from defects or hiccups affect the energy equation? These questions transform abstract numbers into actionable insights.
Industrial DataOps: Turning data into power
In the energy management arena, data's worth is measured by its analytical muscle. A robust strategy demands more than just data collection - it requires weaving together diverse data threads into a cohesive tapestry. Enter industrial DataOps, a game-changer that shatters data silos and amplifies the reach and utility of industrial data, propelling operational excellence.
Industrial giants churn out complex data that craves context. DataOps rises to this challenge, offering a centralized, contextualized truth hub. Its automated data pipelines serve up industrial insights in a language all users understand. This contextualization is not just about connecting dots; it is about revealing hidden patterns. While manufacturers once saw only enterprise-wide or site-level snapshots, DataOps, fusing data analytics with shop-floor operations, now enables product-level granularity.
Take wheat crackers, for instance. DataOps lets manufacturers dissect production data to pinpoint the energy gulped by a 100,000-box batch. If 1,000 boxes are scrapped due to glitches, they can now calculate not just the batch's total energy bill but also the power wasted on defects. This predictability comes from marrying existing OT and IT data connections with asset-centric relationships. All feed into a production data platform where DataOps alchemy turns raw data into gold, spawning solutions for energy management, batch control, asset intelligence, and beyond. With this data core, new apps bloom rapidly, fast-tracking value.
Decoding energy intensity—say, for today's wheat cracker batch—demands a data buffet: raw materials, production stats, recipes, quality checks, and energy sources. DataOps methodically sifts through this data trove, quantifying WAGES usage. It even tracks when that electricity was tapped and its origin - solar, wind, or natural gas. Armed with this certified data, manufacturers can now provide "energy ancestry," labeling products with their carbon footprint in kilograms. It is not just marketing; the European Union will soon mandate such Scope 1 and 2 emission disclosures.
DataOps also illuminates hidden factors swaying energy costs. Night electricity might be cheaper, but does it offset higher third-shift wages? For a plant with hybrid ovens, when should it lean on electric versus gas? Does cranking down summer AC boost quality enough to justify the power surge?
The data finesse honed for energy management also drives other areas. In food and beverage, DataOps might reveal that slower, cooler baking saves more energy without compromising quality. In energy-guzzling sectors like mining or cement, even tiny tweaks from DataOps-driven asset analytics can significantly boost the bottom line.
Charting the course to energy mastery
The quest for energy optimization is not a sprint; it is a strategic marathon. There is no express lane from basic energy tracking to smart management. Manufacturers cannot leapfrog to AI-driven energy control. Instead, the path unfolds in four stages, grouped under two banners: "Visualize & Analyze" and "Optimize & Control."
Picture this journey as climbing a mountain. Stage one is base camp, gathering supplies (data). Stage two is the ascent, analyzing the terrain. Stage three is reaching a vantage point, predicting the weather. Stage four?
You're the seasoned climber, making split-second decisions based on experience.
- Data gathering: First, we cast a wide net, pulling data from diverse sources to craft key performance indicators (KPIs).
- Deep dive: Next, we scrutinize, compare, and contextualize this data. Like a detective piecing together clues, we uncover hidden trends and correlations.
- Crystal ball: Armed with these insights, we craft predictive models. Think of it as energy fortune-telling, where AI, fueled by advanced analytics, foresees future patterns.
- Autopilot: Finally, we enter the realm of prescriptive control.

The roadmap doesn't just show you the mountain; it helps you understand each rock face, optimizes your route, and guides you to the summit. For manufacturers, that summit is low-cost, high-efficiency energy use—achieved through data-driven insights that slash expenses, boost sustainability, and keep you in regulatory good graces.
About The Author
Oliver Haya is a business manager for Data, Hub and Application Platforms at Rockwell Automation. With more than 15 years working with automation customers across industries, Oliver has developed a deep appreciation for the opportunity that better data utilization offers manufacturers. In his current role, he has responsibility for making data available and meaningful to users and applications that can drive business value from that data.
Did you enjoy this great article?
Check out our free e-newsletters to read more great articles..
Subscribe