- By Julian Amezquita and Juan Hoyos
- August 02, 2024
- Feature
Summary
A simple and effective estimation model for flare emissions is key for reducing a company’s carbon footprint and achieving the goal of zero routine flaring by 2030.
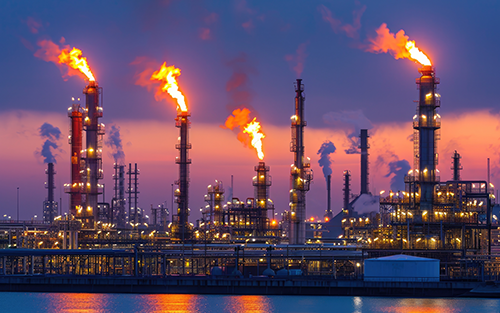
Flare systems are among the most important devices to achieve safe gas release in the hydrocarbon and petrochemical industries. A flare system, alternatively known as a flare stack, is a gas combustion device used in industrial plants such as petroleum refineries, chemical plants, and oil and gas production sites, which during a plant upset or emergency, deals with a flow of waste gas that must be burned completely.
As part of the carbon footprint reduction within zero routine flaring by 2030, an accurate and online measurement of exhaust emissions is necessary to identify the sources of hydrocarbons burned to take actions to reduce their combustion to as low a value as possible. Considering the extensive use of flare systems and their emission composition measurement requirement, a novel digital twin using artificial intelligence (AI) and engineering models merged in a hybrid modeling framework was developed to inference emissions in a flare system (Figure 1).
Methods for emissions estimation
A digital twin is a virtual representation of a system, a process, or an asset, which is developed using engineering models or real-time data. The hybrid modeling framework combines both the engineering models and real-time data from sensors using artificial intelligence (AI) /machine learning (ML) models to create a robust, consistent, and up-to-date view of a process. Since the physical phenomena of flare systems is complex, the hybrid modeling framework is a straightforward alternative to develop an accurate digital twin for emissions inference in a flare system.
Direct measurements, inference models, mass balances, and emission factors are some of the most used methods to estimate emissions of CO2, methane, and other common greenhouse gases produced by a flare system. Direct measurements can be done using special infrared (IR) cameras or space imaging that can accurately determine the composition of gases produced by burning. This method requires a large investment in equipment, appropriate personnel to carry out the task, and is not usually done with enough frequency.
Inference methods using computational fluid dynamics (CFD) allow the online monitoring of the burned gases but require expensive hardware resources for computational power, requiring expert personnel to develop these kinds of solutions.
Oil and gas facilities monitor emissions either by using emission factors or mass balances. Even though these methods are simple to implement and widely recommended by different international environmental agencies, these alternatives have different assumptions such as certain operating conditions or high values of combustion efficiency. These may not always represent all the possible cases and can cause errors in the emission inference.
Digital twin input information
The following information is required to tie the virtual and the real flare systems (Figure 2) for modeling:
- Online measurement of flow, temperature, and pressure of gas to the flare.
- Gas composition to flare.
- Low heating value (LHV) of the gas to the flare.
- Wind speed.
Gas composition and gas LHV to be burned in the real flare are key factors for an accurate inference of emissions in the digital twin. If a chromatography of the gas inlet to the flare is available, it can be used in the model. Otherwise, as usual, it must be inferred inside the digital twin too.
The digital twin of the flare system is built using process engineering models and dynamic simulation software. In the simulation are included all equipment connected to flare headers such as control valves, PSVs, ESVs, BDV, etc. Then from an analysis of the process historic data, new datasets are generated using different cases to represent how the process would behave under different conditions, focused on how the gas inlet composition to the flare would change. With the data obtained, an ML model is trained to predict the composition of the gas to the flare. This model takes as input the most important process and equipment variables that are constantly being monitored in the plant, such as pressure, temperature, and flows, of pressure vessels, liquid storage tanks, distillation and absorption towers, and any other equipment that may affect the gas composition.
The development of this ML model infers the gas composition and LHV as a function of equipment releasing gas into flare and the process conditions to finally obtain the plant emission inference (Figure 3).
The flare digital twin will estimate the CO2 produced (identified as CO2e) from the combustion of hydrocarbons released into the flare; if the gas contains sulfur, SO2 emissions are also quantified, and flare efficiency is calculated.
The digital twin can run on-premise or cloud-based, and two additional features can be added: a forecasting tool and a simulation tool. With the forecasting tool, the real-time CO2 emissions inferred are used to predict the future emissions in the next hour, 6 hours, 12 hours or a time span defined by the user, using time-series analysis. This forecasting allows operators and engineers to take corrective action in case the burning surpasses the defined limits. The second capability is the use of the digital twin directly by the user. This means that the operator or engineer using the digital twin has the option to input their own values of composition, temperature, flow, and pressure to evaluate some special cases for flare emission.
Gas production plant emission inference
The flare digital twin was implemented together with an energy efficiency monitoring system for the amine tower reboiler and the heater for the heating oil.
The SIMATIC Energy Manager V7.4 software by Siemens, was used for on-premises deployment of the solution in the plant servers. The connection is done via a local OPC-UA server, which retrieves the client’s programmable logic controller (PLC) data and the historian data. From the OPC-UA server, the data is sent to the flare digital twin developed using the Python programming language. The digital twin computes calculations and sends back the results to the OPC-UA server. The energy manager application takes the flare’s system digital twin results and adds them to the additional data for the energy efficiency calculations and displays the visualization of the results in its interface for use to the operators and the engineers of the gas plant (Figure 3).
Results
The digital twin was allowed to identify the state of the emissions in the gas production plant. Figure 6 presents the hourly emissions of CO2e from 1 August 2023 to 4 September 2023. The gas was emitting an average of 1 metric ton of CO2e per hour, represented by the red line in the graph, with a minimum of 0.018 tons of CO2e and a maximum of 4.92 tons of CO2e. The average emissions were heavily affected by the spikes. Even though at the beginning of the analysis, it was supposed that the spikes represented the activation of safety valves, PSVs, etc., by further inspection it was found that the last security valve opening was three years ago, and that the emissions generated from the plant come from another source.
The source of these emissions is by the fact that the gas already treated is sent to the generation plant nearby, but before leaving the plant, it passes through a pressure control valve (PCV). When the pressure of the gas exceeds a value of 410 psig, the valve opens due to overpressure, and the gas is sent to the flare. This overpressure is happening due to a newly constructed solar farm in the region. This farm supplies a portion of the electrical energy used in the region and the other portion is produced by the thermoelectric plant that receives the natural gas from the gas production plant.
When the solar farm is at full power, the thermoelectric reduces its consumption of natural gas, which causes an increase in the transport pipe’s pressure until it reaches the gas production plant outlet. Because there is no way to store the produced natural gas or to send it to another plant, the increase of pressure is such that it passes from the normal operating conditions of 385 psig to 410 psig, the PCV then opens, and the gas is sent to the flare to avoid accidents. The solar farm has the purpose of producing clean energy from a renewable source and decreasing the CO2e emissions. But when the farm is at full power, it causes additional burning of natural gas that translates to an increase of CO2e emissions that wouldn’t occur in the plant under normal operating conditions.
Final thoughts
The flare’s digital twin allows constant monitoring of the emissions in the plant. Being a tool for identifying opportunities to decrease emissions and to make the appropriate decisions, it serves as a soft sensor and is a solution that is much cheaper than the implementation of a physical sensor or a continuous measurement using cameras or even more complex inferences using CFD.
In the pilot project presented, this online monitoring helped to identify how the emissions are behaving, and through the analysis of the data and the interviews with the operators, a problematic circumstance was found that is increasing the emissions of the plant. The use of the digital twin as a soft sensor allowed the identification of this situation but also gave enough information for taking the appropriate corrective action.
Finally, an advanced process control (APC) optimization algorithm is in the implementation phase in the gas plant. When commissioned, the next step is using the flare system’s digital twin to obtain insights on how the optimization affected the gas production plant emissions if a reduction is obtained, or what additional measures must be taken.
References
1. Bahadori, A. (2014). Blow-down and flare systems. In Elsevier eBooks (pp. 275–312). https://doi.org/10.1016/b978-0-08-099971-5.00006-4
2. Wakil, W., “Minimize Flaring in Oil and Gas Facilities”, Chemical Engineering Progress (CEP), p. 22 (Jan. 2023).
3. What is a digital twin? | IBM. (2023). https://www.ibm.com/topics/what-is-a-digital-twin
4. Abbas, A., Guevara, V., & Romagnoli, J. A. (2002). Hybrid modeling: architecture for the solution of complex process systems. In Elsevier eBooks (pp. 409–414). https://doi.org/10.1016/s1570-7946(02)80096-7
5. Emam, E.A. (2015). GAS flaring in industry: An overview. 57. 532-555.
6. New and Revised Emissions Factors for Flares and New Emissions Factors for Certain Refinery Process Units and Determination for No Changes to VOC Emissions Factors for Tanks and Wastewater Treatment Systems | US EPA. (2022, December 19). US EPA. https://www.epa.gov/air-emissions-factors-and-quantification/new-and-revised-emissions-factors-flares-and-new-emissions
About The Author
Julian Amezquita is technical leader of research and development for West Advanced Solutions LLC. He has experience in dynamic process simulation and implementation of APC solutions for oil and gas facilities and is responsible for the development and implementation of digitalization and industry 4.0 projects, products, and solutions for the process industry.
Juan Hoyos is an industrial data scientist in the research and development office of West Advanced Solutions LLC. He specializes in the application of data science, machine learning, AI, and hybrid models for process modeling and simulation in the oil & gas and bioprocess industries. He is also responsible for the integration of AI and ML in the digitalization solutions developed by West Advanced Solutions LLC.
Did you enjoy this great article?
Check out our free e-newsletters to read more great articles..
Subscribe